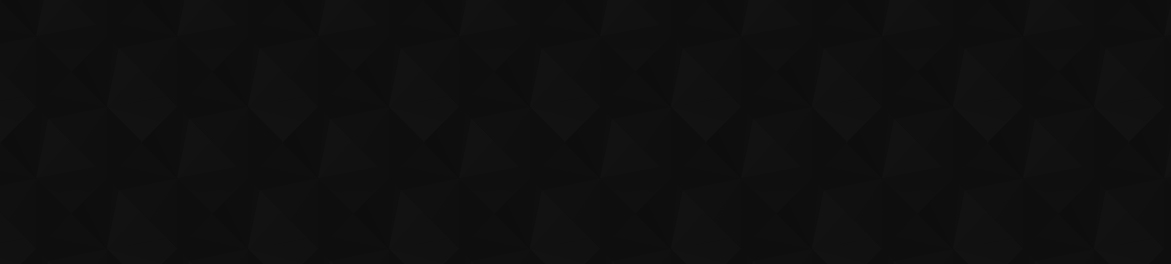
- 290
- 672 134
Tyler Harney
United States
Приєднався 18 кві 2010
Відео
Laser Cutting Main Panel with Walk Around
Переглядів 274Місяць тому
Laser Cutting Main Panel with Walk Around
Cutting some round pedestals and stuff
Переглядів 41Місяць тому
Cutting some round pedestals and stuff
CNC - Sports Water Bottle UV Printer Jig Version 2
Переглядів 3362 місяці тому
CNC - Sports Water Bottle UV Printer Jig Version 2
4x8 vertical laser cutting a window exhaust fan mount.
Переглядів 625 місяців тому
4x8 vertical laser cutting a window exhaust fan mount.
AVID CNC, 4.5kw ATC Spindle, 30mm(1.2 inch), Reinforced Globulous Birch Plywood
Переглядів 7866 місяців тому
AVID CNC, 4.5kw ATC Spindle, 30mm(1.2 inch), Reinforced Globulous Birch Plywood
Masso G3, AVID CNC, 750w DMM-Tech Servos, 100w laser tube.
Переглядів 5166 місяців тому
Masso G3, AVID CNC, 750w DMM-Tech Servos, 100w laser tube.
I have a Onefinity elite. Did you get a file for the letters? I’m brand new to cnc. Just assembled it and I’m looking for my first project. Any tips you can share would be greatly appreciated. Thank you for sharing this video.
Welcome to the world of CNC! :) So I had originally bought the letter pack on Etsy from DIYWeddingMarket and they supplied the SVG & DXF files that I could load into my CAM program. I did make one modification to the holes and replaced their basic round holes with my design to hold the light socket perfectly. As far as tips, Compression bits are 100% worth it. Just remember compression bits should never plunge into the material, it needs a zig zag/ramp lead in feature. Use conventional milling (right hand) when cutting contours/profile cuts in wood. It is entirely possible to cut a single full depth of cut on a 1/8" compression bit through plywood and MDF. The GWizard program that calculates feeds and speeds is a life saver to figure out those feeds and speeds. Looks complicated to a newbie though not gonna lie. First projects that I started out doing, simple signs. Pocketed out letters and a simple contour sign cutout. Then got into Vcarved signs. Let me know if you have any other questions.
The cradboard is 5mm?
Just measured, it's 4mm thick
Simply magnificent Tyler, excellent work 🎉🎉
Que tipo de socket utiliza
C7 Bulb Sockets SPT-1 - amzn.to/3XE6kiz
lot of people wont understand but great job, keep up
Z sensor?
How it is done?
There's any way to get part list for laser head and optics
This was the kit I purchased. Came with the whole laser head assembly, mirror, lens, the motor driver and the sensor control board. lightobject.com/real-time-auto-focus-laser-head-rtaf/
ありがとうございました。
Hey, can u tell me whot spindle do u have ? Model.
I have 4.5KW (Model A) ATC Spindle ISO30 220V from NewCarve. I only had one issue within the first 3 months and that was the top fan died out. I didn't bother trying to get it replaced over warranty so I bought a new fan & replaced it myself. www.aliexpress.us/item/2252799820443576.html?pdp_npi=4%40dis%21USD%21US%20%241%2C438.00%21US%20%241%2C222.30%21%21%211438.00%211222.30%21%402101ea7117349033081231428e377f%2112000043182962113%21sh%21US%21127237761%21X&spm=a2g0o.store_pc_allItems_or_groupList.new_all_items_2007550666904.1000006758328&gatewayAdapt=glo2usa
🤪 Thank you. Actually, I'm getting the schematics from the link. I'm buying the controller on Amazon and don't provide schematics. Thanks
Hi Tyler Congratulation you did it ,what was the problem?, the parameter of the controller or another issue? . I only log on once a week for a little while Tyler, for that reason sometimes I don't answer but when I log on I catch up
EDIT: So the issue you're referring to, the skipping, yeah it was the parameters issue. Shortly after though, which I don't think I have updated you on, while that did fix it, I started getting my Y2 servo drive faulting out due to "over heat" (the shop was COLD af and the driver was cool to the touch.) Wellll I kinda didn't fix it. I had thought I did, cause I switched out servo drives (I had an extra from my router build). That new drive worked ALL weekend until I tried engraving something. Exact same issue happened, the new drive faulted out to "overheat". Odd behavior. Same exact settings as Y1 driver. So I think I'm going to swap the entire Nema 34 DMM-Tech servo system to regular AC closed loop stepper motors/drives from Automation Technologies Inc and hold these servos for my PM-940V milling machine I'm about to order before the new year. I have the closed loop stepper system on my 4x8 router and haven't had any issues for the past 4 years so I'll make it work. Servos are more of a headache to be honest, especially with a gantry machine and the need to auto tune 1 motor at a time with the DMM Tech servos.
@@TylerHarney Thank you very much for sharing your experience Tayler 👏👏🥇🥇, that helps us all to know what can happen to us when we build our own machines, I really appreciate it, your designs also help me think of things to implement on my machine, thank you very much for all your tips Tayler, I don't use servos, but if I use them thanks to you, I already know the possible problems I may have. Keep it up, Tayler, as always, congratulations ,have great success with your future creations and have a Merry Christmas.
@@Mekaproyects <3 MErry Christmas Meka!
Hello, an idea occured to me (maybe it has to you as well).If your goal is to create an optical contrast, you could cut the same sketch on a dark wood panel and switch the cut-outs. So you will have a light fond with dark rectangles, and a dark fond with light rectanglesand use all the cut-outs. Just an idea. Have a nice day!
I didn't think about that on this project, but I like that idea! I'll have to keep that in mind for the future. Thank you!
The tube on the gantry is a cool idea... increase cutting envelope regardless of tube power...
While planning that out I realized that if I left that extra extrusion overhang I could remove that 1st mirror which would make the beam pass through and I'd mount a laser head at the end of the extrusion. Then I could mount a 4th axis rotary chuck allowing me to cut cylindrical pieces along the Y axis. I've got the rotary chuck but haven't yet started the design add on yet.
you wind some you lose some. lol. thanks for sharing the failures too.
I had plenty of them this past weekend. It's weird, everything seems to break or mess up when I start recording. Thanks for checking out the video!
With this image you can see how it made totally erratic cuts, nothing to do with the original file, with small files it had no problem, I hope this information can be useful to you at the time. I also tried everything but I myself caused the failure by moving the controller parameters too much.
Hello Tyler, I had a similar problem and it was that I moved too much to the factory parameters of my controller, so it caused strange cuts. I'm going to share with you an image of how a file was wrong. Only some large files failed, not all of them. Check if the same cutting error that you get physically on the piece appears on your controller screen. If so, then you have to lower your parameters to a point where the machine remains stable. My advice is to save the failed file and run it with different parameters without physically cutting it. Let the file that has the error run right now but without connecting motors or anything, wait for it to finish and check on the controller screen if the error disappears I had to lower the acceleration and speed parameters, it was trial and error because each machine is different, but first I returned everything to the factory parameters and started testing by lowering the parameters until the failing file no longer failed. I'm currently saving this file in case I build another machine in the future and need to check it. I'm going to look for the image and share it with you Tyler
!! I did take notice of the screen with the failed file. I didn't think anything of it except it was just super weird and I kept debugging.
Hello Tyler, I had a similar problem and it was that I moved too much to the factory parameters of my controller, so it caused strange cuts. I'm going to share with you an image of how a file was wrong. Only some large files failed, not all of them. Check if the same cutting error that you get physically on the piece appears on your controller screen. If so, then you have to lower your parameters to a point where the machine remains stable. My advice is to save the failed file and run it with different parameters without physically cutting it. Let the file that has the error run right now but without connecting motors or anything, wait for it to finish and check on the controller screen if the error disappears I had to lower the acceleration and speed parameters, it was trial and error because each machine is different, but first I returned everything to the factory parameters and started testing by lowering the parameters until the failing file no longer failed. I'm currently saving this file in case I build another machine in the future and need to check it.
ভাইয়া ডিভাইস ফিউজ ডিসকানেক্ট এখন কি করিতে পারি পরামর্শ দেন
I think you should seriously consider eye protection when operating this way.
I would agree. I do have plans on covering the beam path.
Hi Tyler, congratulations, you are very creative, I like to see your machine designs, thank you very much for sharing your ideas, have an excellent day
I didnt know this was something you could do! Thats awesome!
did you use a box design tool or is it your own design? I have been thinking about making boxes too. thanks for sharing
I used the Fusion360 sheet metal feature to design the box. Then for the bends I lasered as a perforation.
🤣🤣🤣🤣 A esto en mi pais se le llamaría tener unos cojones como un caballo!!!!!👏👏👏 No te preocupa que el movimiento acorte la vida del laser??
Ha ha! I knew someone would say something 🤣 I've made much progress since this post. Let me upload my newest video I took this week cutting the same cardboard boxes. I stripped the Masso controller, the entire gantry and designed a lower center of gravity gantry with a servo belt drive X axis.
ua-cam.com/video/j3x2nIH47ig/v-deo.html
What for is that shit? Why do I see that pointless stuff?
huh?
Hello, where can I get the module?
Signal Generator: amzn.to/40w82Es Stepper Motor: amzn.to/492FLbS Stepper Driver: amzn.to/3RxAMbC Power Supply: amzn.to/48JOU9D
Is it 1 or 2 flute compression bit?
2 flute, I just used a cheap amazon bit. I bought 10 of them cause I didn't think they were originally up to the task. amzn.to/3Zpmobf
Well done!
Thank you! I want to remake it out of some baltic birch. Then the small pocket tags at the bottom of each tool will be a dual color 3D printed ## insert. Version 2 might be cool if it was fully enclosed with an acrylic front window. Then you have a staging tool holder at the front of the machine where you put your tools for that particular program you are about to run.
are there laser cutters in the less than $350 range that could cut sheet steel or aluminum to make custom metal dashboards in autocross cars?
No, You'd be better off buying a CNC router to cut those dashboards. You would need to stick to aluminum. As far as steel, a plasma cutter CNC could do the job. As far as cutting steel or aluminum using a fiber laser, those machines start at at least $20k and use 1.5-3kW of power. 150w-300w CO2 laser can cut carbon steel but you're still looking at $25,000. The tubes alone could cost $4k. Hopefully that helps. A cheap CNC router using the correct endmill cutter and feed/speed could get you started.
I just cut out 10 beautiful gaskets for my Monarch 10EE lathe oil sight glasses out of 1/16" buna N / cork gasket material using the same blue 50 watt type laser as the OP. For reference I used the same 20 speed but used 55% power and it worked great. The smell of burning rubber is VERY strong and strong ventilation is an absolute requirement. For reference I believe that a good air assist is also necessary to cleanly cut through cork or cork/rubber material. The lack of a good air assist in the K40s or similar may be why some of you are having trouble with cork.
Hello! What kind of bit did you use?
This is the bit I use. It's a compression endmill so I can take a single pass. amzn.to/48z46qX
If you want to first try a bit that's cheaper that cuts the same, amzn.to/3NOSMgv
hey just use another material. i would like to buy the table
Shoot me a message over on my website under the contact section. I'll be able to accommodate.
Appreciate this information very much buddy, thanks for taking the time. All the best to you
It can't rotate reverse direction when full speed condition. Why and how to resolve it?
Nice looking parts! Especially considering you appear to have the taller gantry on your Avid. Also, I think "globulous" might be my new favorite word for a while.
Thanks! This was a project I did for Lollapaloose Chicago 2024, I design/fabricated a pair of high top Charging Tables for Coca Cola with a 3 tiered Govee lights around it. Ha, it is an interesting word. Yeah I've had absolutely 0 issues with the taller gantry. Now on my second machine, I have the taller gantry and extended, I do notice a very noticeable wobble. The only difference in the frame, I see, is my first machine uses the steel 45 degree leg supports and my second machine uses the aluminum 45 degree leg supports. I do have servos on the second machine so that could be making the difference too. DMM doesn't have a way to tune the two gantry motors very easily so I'm kinda guessing.
Can you be more clear where the 5v comes form I am using the MD556 stepper driver with the very same controller shown in your video... thaks
Do stepper motors run cooler with driver is set to less steps per revolution? Do stepper motors run cooler with driver is set to less Amps? I am using Nema 23 57x57x56mm, 23HS2430B, 57BYGH056 Using DM556 Driver ZK-SMC01 stepper motor controller AC 110v to 24v Power Supply 20A Max Using on a machine that runs for hours at a time. Motors run feed screw at constant speed one direction then the other direction for 10 minutes before reversing then repeats. Driver is now set to 2.7A -1600
323 / 5.000 wooo you just invented something new, very creative and more efficient since you do not lose power through the mirrors and you eliminate the need to calibrate the entire path, in addition to other advantages inherent to your design, many congratulations Tayler, it is an invaluable contribution to the world of laser cutting, you are brilliant. 😁😁
Thank you, Thank you! I do notice an increased amount of available power with this tube only firing through the lens and bypassing any type mirrors. I'm pretty excited :)
@@TylerHarney
Any more info on how you set this up?
I'll take some more videos. I designed a 1/4" steel tube mount that bolts to the AVID Z axis plate. The power supply is mounted to that tube mount. I also stiffened up the back of the Z axis assembly. I turned some steel down to create a mount for the lens head. I'm using Masso's Pin 11 PWM output, pin 12 turns on the air assist which is plumbed in from my compressor. I DO have some noticeable EMF that may drive people away from the project. I'm not sure if it's the way I have the signals set up to the laser power supply or because I have a 110v power cord running through the machine up to the laser power supply or if it's Masso's PWM output issue. I cut my first 1/4" acrylic parts last night and am super impressed with the edge quality despite some noticeable vibration from my 12" gantry height. Either that or my servos need further tuning. The edges were super smooth, these were rectangular parts tho. I do plan on cross bracing the legs as well. It's weird, my first avid is much more rigid than this second one.
woah.........
Hello bro , l have got same problem but in case of showing error code (fu.13) it's showing error code (fu.37) please tell me the reason why it's showing like that
What are the dip switches set to?
Don't remember, but probably 1600 steps and whatever amperage that motor was rated for.
Is that going to go on the metal one?
Maybe, if that ever gets done. Focus has shifted to the 4x8 laser at the moment. I'm doing this same set up for the main CNC router. Since that laptop is on it's last days.
might I ask what diameter is the maximum you can insert into the ER11-Collet? 7mm or 8mm?
I believe it's 8mm max diameter.
you must be surfacing the spoilboard quite a bit with all the coolant soaking into the mdf
Hello Tyler, I'm asking you, I have to carry out the same project but the Nema motor always has to rotate in one direction, could you guide me on how to do it and if I need other components, thank you
Sorry for the delayed response, You could remove the direction signal wire. I'm pretty sure that would only make the motor move one direction.
Hello friend, thanks for your video. I made the same connections with a nema 17 motor + a 12v power supply and a tb6600 controller. It works, but it doesn't spin as fast as yours. What I can do? Microstep settings? or could it be something else? thank you.
Hey J, Most likely the microstep settings
Hi, would a diode laser be able to cut this?
I think so.
ciao si puo avere il file ?
No way
No way, what? lol